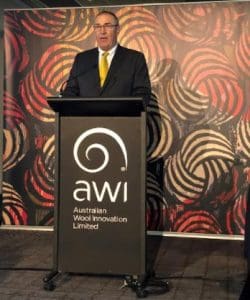
AWI chairman Jock Laurie at the 2021 annual general meeting. Image – AWI.
RAISED shearing platforms, chemical defleecing, sheep handling innovations and cross-industry collaboration will be considered as Australian Wool Innovation looks to solve the industry’s labour crisis.
Despite expected relief from ag visa worker developments and rebates on backpacker visa fees, the impact of COVID-19 worldwide and domestically on cross-border movements has continued to exacerbate the nationwide shearer and shedhand shortage.
AWI chairman Jock Laurie said the company has already done and was continuing considerable work on shearer and shed hand training to overcome the industry’s labour shortage.
“For the last four years we’ve been prepared to invest in anything that would try to help rectify this problem.”
But Mr Laurie said AWI and the industry had been unable to come up with any innovative ideas, domestically or internationally, to really overcome the problem.
Click here to see details of AWI’s wool harvesting and training timetable.
Need to concentrate more on upright shearing
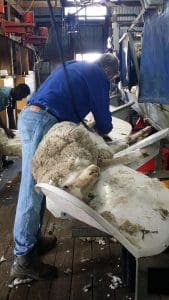
A sheep being shorn on Burbidge platform.
Mr Laurie admitted AWI needed to further concentrate on the option of upright shearing platforms, as developed by New South Wales grower Grant Burbidge, while it continued to do as much shearer training as it could.
Mr Laurie said he has spoken with Mr Burbidge about the shearing platforms and viewed his video, and he believed people from AWI had “engaged in this space.”
“But from a company and industry point of view we need to invest in multiple options.
“It will be upright shearing where we can use new unskilled labour and train them in upright shearing platforms, we can continue to train and expand the training we are doing,” he said.
“This is about getting sheep shorn, management of flies and general management issues.
“If we are talking about getting sheep shorn on time, we need to provide multiple tools, multiple options – whether it be Bioclip (chemical defleecing) if we can use that, platforms, training, new sheep (catch and drag) delivery systems – a whole range of things to make it easier.”
Mr Laurie said AWI is already investing in many of the options he listed.
“As a board we have got to sit down and have a serious discussion about this and that will be happening at the end of the week.
“We really need to understand where the pressure points are and I’ve asked the company to do some work there,” he said.
He said the industry might need to look at whether shearing times in some areas is an option.
“We’ve already been doing, with the Wool Industry Consultative Panel, work with the government in regard to COVID issues and getting overseas workers in.”
Mr Laurie said AWI hasn’t had any success in finding viable options outside the conventional shearing industry to solve the wool harvesting problem.
“If somebody came to us with something that could break this, we are prepared to invest in it.
“The company has always been prepared to invest in good ideas that could actually change the dynamic when it comes to shearing.”
Mr Laurie said the broader industry also needed to “step up”, with contractors and flock owners being prepared to put on learner shearers, and shed and accommodation conditions need to be “up to speed” to attract and keep workers.
The AWI leader said AWI is also ready to collaborate with other levy-funded organisations such as Meat & Livestock Australia and Animal Health Australia in implementing solutions.
“We will work with anybody and everybody that wants to work with us in a collaborative way that wants to work with us.”
I spent ten years of my life swinging around on the end of a downtube and always thought there must be an easier way to shear a sheep. So eight years ago I started to build a shearing table. I was very lucky to have a clever engineer by my side and we started of using pneumatics for all controls, but ended up with electric hydraulics. I always said that it would have to be quicker than conventional shearing. If not, I would be wasting my time. Have had a couple of sheep over it and it is looking good hope to have it going in a couple of months time.
Please, please, please, bring back Bioclip. As a small landholder with mixed breeds, I have a growing number of sheep to shear each year.
I have managed to find a couple of ex-shearers in the past. It has been costly, time consuming and stressful. No-one wants to come and shear a small number of sheep in my area. I think shearing is a very skilled profession, and shearers deserve a lot more money and recognition.
I just get by now with a decent Heiniger clipper. It’s really hard work. My sheep end up looking like a rag tag bunch.
I wish I had the luxury of choice and was able to choose Bioclip. I can’t believe it was taken away. What a convenience it would be.
Re: Bioclip. I have been told by someone who worked in the space that the system was bought by Heiniger and locked away. If AWI invested in it hopefully it can be resurrected.
I believe that AWI should do a cost benefit analysis of the most profitable wool-growing enterprises in Australia, to identify what the key profit drivers are. This may find that shearing less than annually doesn’t help the bottom line. If my assumption is right, this could free up heaps of skilled labour to benefit an industry that is on the ropes.
Since the mid-1970s, I saw first-hand and reported on just about every piece of research option to replace or complement conventional shearing – chemical shearing, robotic shearing, shearing tables and the big daddy of them all ShearExpress. The reality is that nothing has been able to beat the conventional shearer for cost or efficiency.
The hard truth is that if the industry wants to attract shearers it has to lift the pay rates and improve shearer conditions. There are too many other easier employment options and often at better pay rates.
If you can’t find or encourage shearers, Merinos and AWI will both be in a death spiral.
Lots of stock agents are making $10,000 in commission at every saleyard sale, while the shearing rate and shearers’ cheques haven’t increased by comparison. It’s easier drafting lambs for sale than shearing them. With the shearing platforms, I’m sure contractors would have invested in them if there was a dollar to be made. It’s like Shearezy, about $15 a ram, I’m told. Offer your shearers that and most would relish it. It seems about 150 a day can be shorn on the platforms. So the rate would need to be about $6 a head, almost double the current shearing rate to achieve a wage comparable to across-the-board. The bigger operations still have contractors competing on price, charging $200 for a killer and rouseabouts paying full mess.