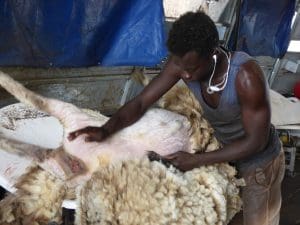
Abe Gwada shearing at Hawkesdale in south-west Victoria.
NEW South Wales wool grower Grant Burbidge didn’t have a career as a shearing contractor on his agenda.
But after shearing his own sheep with upright sheep shearing platforms that’s exactly what he has become to wool growers and sheep meat producers seeking to harvest their clips without relying on conventional shearers.
“I turned 60 last year and it certainly wasn’t in my life plan to become a shearing contractor at any stage.”
In the past 18 months, Mr Burbidge said his shearing teams have shorn nearly 50,000 sheep with the moulded fibreglass platforms, which are based on the Wytkin upright position shearing platform from Western Australia.
The sheep are fed into a race erected just above waist height inside a conventional wool shed and are tipped from the race into the concave fibreglass cradles and also held by one back leg hook. The shearer leans across the sheep to shear it and is able to remove and discard stain, pieces or dags from sheep into a nearby bin without losing control of the animal.
Grant and Annette Burbidge have employed young people who never would have taken up conventional shearing, but also saved them from dragging hundreds of tonnes of sheep across shed boards. Right-handed shearers learn to switch to their left hand to do the first back leg.
“We’ve shorn Merinos, crossbred lambs and those big composite ewes, rams and Merino wethers,” Grant said.
The sheep shorn have weighed in as light as 25kg for Merinos and up to 100 kg-plus composite ewes and rams. Crossbreds are more active in the cradles.
“Everybody who comes into our shed while we are shearing the Merinos says ‘I can’t believe that they just lie there and get shorn.”
Click here to get the latest Sheep Central story links sent to your email inbox.
Wool growers need a reason to use platforms
Grant said probably the most difficult thing was trying to get some decent materials to make the shearing platforms or cradles.
“If I could get an order for 200-300 you would go to injection moulded plastic – 500 platforms would be nearly enough to do 20 percent of the Australian clip.
“My estimate is that you need about 3000 of these units to shear the whole Australian clip.”
Shearing cost under $5 is possible
Grant said there had been many inquisitive wool growers, but not a lot of demand to use the system since he first shore his 22,000 Merinos over platforms in 2015.
“There has got to be some catalyst for people to change from their current teams and that catalyst might be because they won’t shear them because they are too big or maybe for some reason your team has disbanded, like ours did.”
Grant is not promoting his platform shearing system as a cost-saver, because it depends on how people want their wool prepared and conventional shearing costs can vary from around $5 a sheep to up to $8 in contract rates.
With the cost of training “a heap of people who never persisted”, the Burbidges costed their first platform shearing at about $7.30 a head, but this was reduced at the last shearing with the use of previously trained staff.
“We have also got a lot better at recruiting and training people which has greatly reduced the staff turnover.
“Once I can phone and get a team of people who have already used the system, it will be below $5, but that doesn’t mean that’s what it would transpire for everybody.”
System is a ‘no-brainer’ for OH&S
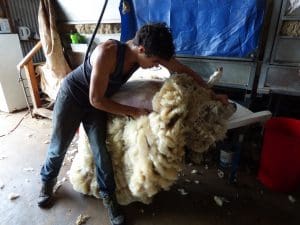
Platform shearer Ryan Cotter at Hawkesdale.
The Burbidge shearing team has done a couple of contract shearing jobs in New South Wales and Victoria in 2016-17 and has also been used for crutching.
“Those who want to try it, just want to do a few sheep and give it a go – they don’t want to upset their current team in case it doesn’t work.
“This system does not make shearing easy, however it does make it easier,” he said.
“I think it is a no-brainer, simply because of occupational health and safety, at the end of the day whether it’s my sheep or someone else’s, there is six tonnes of sheep the shearer hasn’t had to drag out for the day.
“And in the case of Phil O’Toole at Hawkesdale, it could be 10 tonnes of sheep that the shearer hasn’t had to drag out, Grant said.
“So if the shearer is doing 120 a day on Phil’s sheep it would be 10 tonnes of sheep they would have to drag out over the board, whereas with this system they don’t have to do that.”
Sheep could also be shorn in the cradles after as little as four hours off feed and water, although 12 hours would be better.
“In hot weather curfews of 36 hours are just ridiculous, from a welfare point of view you shouldn’t be doing that,” Grant said.
Beginners shear more sheep earlier on platforms
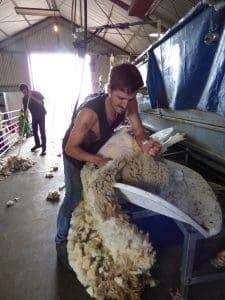
Beginner shearer Conor Madden at Hawkesdale this month.
Except for four conventional shearers who have used the platforms, none of the 20 people Mr Burbidge has trained would have considered shearing conventionally, he said. Only one of the conventional shearers liked the system.
“Platform shearing is not new, the earliest reference I can find is in the 1940s, but every system so far has failed and the main reason is because they have tried to use existing shearers on the new system.
“Conventional shearers are highly skilled at a process; however, if you change the process, they are no longer highly skilled at all of the new process – they’ve got to learn again,” Grant said.
“My experience with conventional shearers on this new system so far is that most of them are not willing to go through that learning phase to get to the same stage as they are at with conventional shearing.”
Two shearers shearing at Phil O’Toole’s property at Hawkesdale in western Victoria this month had never used a handpiece before, and one, Conor Madden, 25, was able to shear 102 sheep a day after just eight days.
“In a conventional system there is no way that anyone would do those 102 sheep in a day starting from scratch.”
Grant said he had not sorted out all the issues with platform shearing, but the system will develop and he has designed it to go into a trailer.
“This has been a self-funded quarter of a million dollar project for us and before we spend another $100,000 on a trailer you would want to know that you had someone to buy or use it.”
There have been numerous industry attempts to develop other platform shearing systems, including the abandoned Shear Express trailer and the SLAMP (Sheep Loading Animal Manipulation Platform) system being used for crutching in Western Australia. But Mr Burbidge believes for his system to develop it simply needs to be used.
“You have to have demand, but I don’t have to prove that it works all over the place and have it accepted by the whole industry.
“My aim is to be able to shear my own sheep and to have a supply of trained people to shear those sheep.”
Training and retaining staff is main restriction
Grant said the main restriction on wider use of the shearing platforms is training and retaining staff to use the system.
”If the industry wants to adopt this system then someone else in the industry is going to need to fund the training process.”
Shearers using the Burbidge platform system can be paid an extra 50 cents per sheep to remove pieces from a fleece before continuing shearing, effectively saving cost, but the system can incorporate traditional wool handling and clip preparation.
“The biggest inefficiencies in a wool shed are not with the shearing, they all relate to movement of the shed hands.
“Picking up a belly and taking it and putting it in a bin, or picking up a fleece and taking and throwing it on a table and then the rollers have got to find where the cotted jowls are … they’ve got to go looking for what they’ve got to take off, whereas the shearer can get all that as he or she goes, that’s where the efficiency is, it’s in the wool handling,” Mr B
In the Burbidge shed, there are four presses operating; one for the sound and tender fleece lines, the third for pieces and the fourth is kept empty for when a bale is filled mid-run.
“The four presses really has revolutionised our shed; it has taken a lot of labour out of it.
“Putting stuff in bins and then getting it out again is a complete waste of time,” Mr Burbidge said.
Interesting, but a few contradictions. They obviously sit better in the cradles when empty. I know when drenching sheep if you get them in the night before, they don’t fight as much. Their gear didn’t look to be cutting real good in the photo. But to have a raw learner doing a hundred after a couple of weeks is a really good effort. Our bodies weren’t designed to bend over for eight hours a day, but they look to be bending over a little bit, so long-term operators would probably have the same hip, shoulder, wrist and elbow problems as in conventional shearing. At least they have it operating without getting millions of dollars out of our compulsory wool levies.
Great story, is there an email or phone number for Grant Burbidge please ?
Very interested.